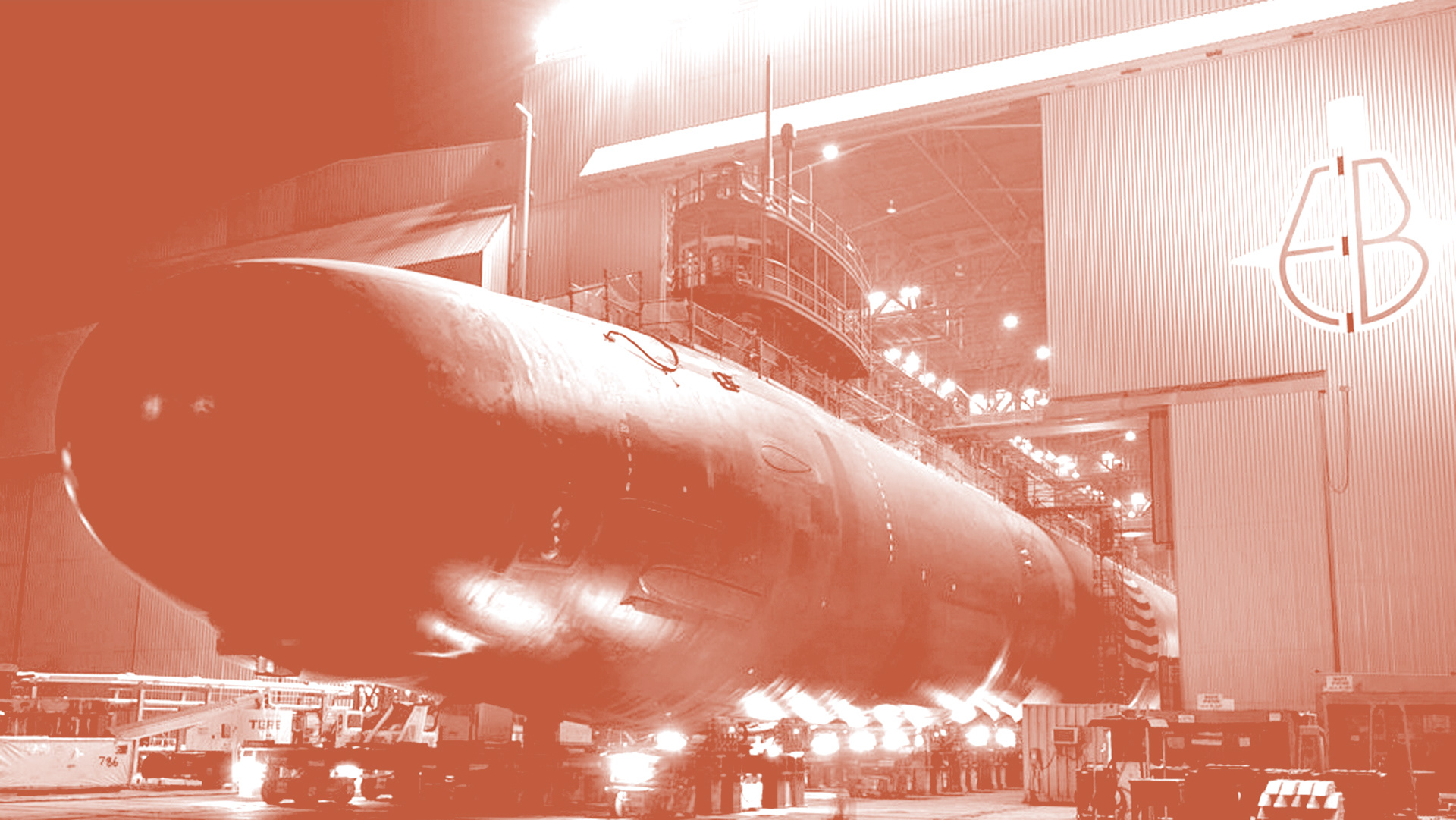
The Background
Shipyard workers endure long hours on their feet, standing on hard concrete and working with heavy steel. These physically demanding conditions are further exacerbated by the reliance on paper-based instructions. The combination of strenuous labor and cumbersome, lengthy manuals underscores the need for a more streamlined, efficient digital solution in the submarine construction process.
General Dynamics Electric Boat (EB), a division of General Dynamics, approached our User Experience organization to enhance their submarine construction process. Traditionally, this process relied on extensive paper-based work instruction packages, each spanning 60 to over 200 pages. These lengthy documents were not only costly to produce but also posed challenges in version control and lacked an efficient method for tracking revisions.
In January 2023, the Government Accountability Office reported that issues with work instructions and late materials were contributing to construction delays. Problems with work instructions—detailed design products that describe how to construct the submarine—including poor quality have primarily resulted from inexperienced planning staff. Material availability—timely delivery of components to the shipyard—has been strained by supplier and shipbuilder manufacturing delays.
To address these challenges, EB required a tablet-based application for shipyard tradespersons to streamline submarine building. This digital solution aimed to replace cumbersome paper instructions, thereby improving efficiency and accuracy in the construction process. Given that EB employs a workforce of approximately 19,500 individuals, including 13,400 in Groton, New London, and Stonington, Connecticut, this initiative had the potential to impact over 10,000 tradespersons daily.
· EB anticipated not only reducing production costs and minimizing delays but also enhancing version control and revision tracking, leading to a more streamlined and efficient submarine construction process.
THE OBJECTIVE
The objective of this initiative is to enhance operational efficiency and reduce production costs by transitioning from traditional paper-based work instructions to a tablet-based digital application. This digital platform will consolidate extensive text and engineering drawings into streamlined, task-specific displays, presenting only the essential data and 3D graphics required for each operation. Implementing digital work instructions has been shown to improve line efficiency and ensure a high level of quality with every product that comes off the line.
THE CHALLENGE
Traditional paper-based work packages contained detailed, step-by-step instructions, with a typical 20-hour task spanning around 60 pages. Tradespersons frequently had to flip back and forth within these lengthy documents, cross-referencing key details from earlier pages to complete each step accurately.

Converting this process into a streamlined digital experience required a solution that preserved critical context while improving usability, efficiency, and real-time accessibility.
Our Process
I led a user-centered design process to streamline submarine construction by transitioning from cumbersome paper-based instructions to a tablet-based app. Through Discovery, Design, and Evaluation, we assessed existing workflows, developed intuitive prototypes, and conducted user testing to enhance efficiency for over 10,000 shipyard tradespersons.
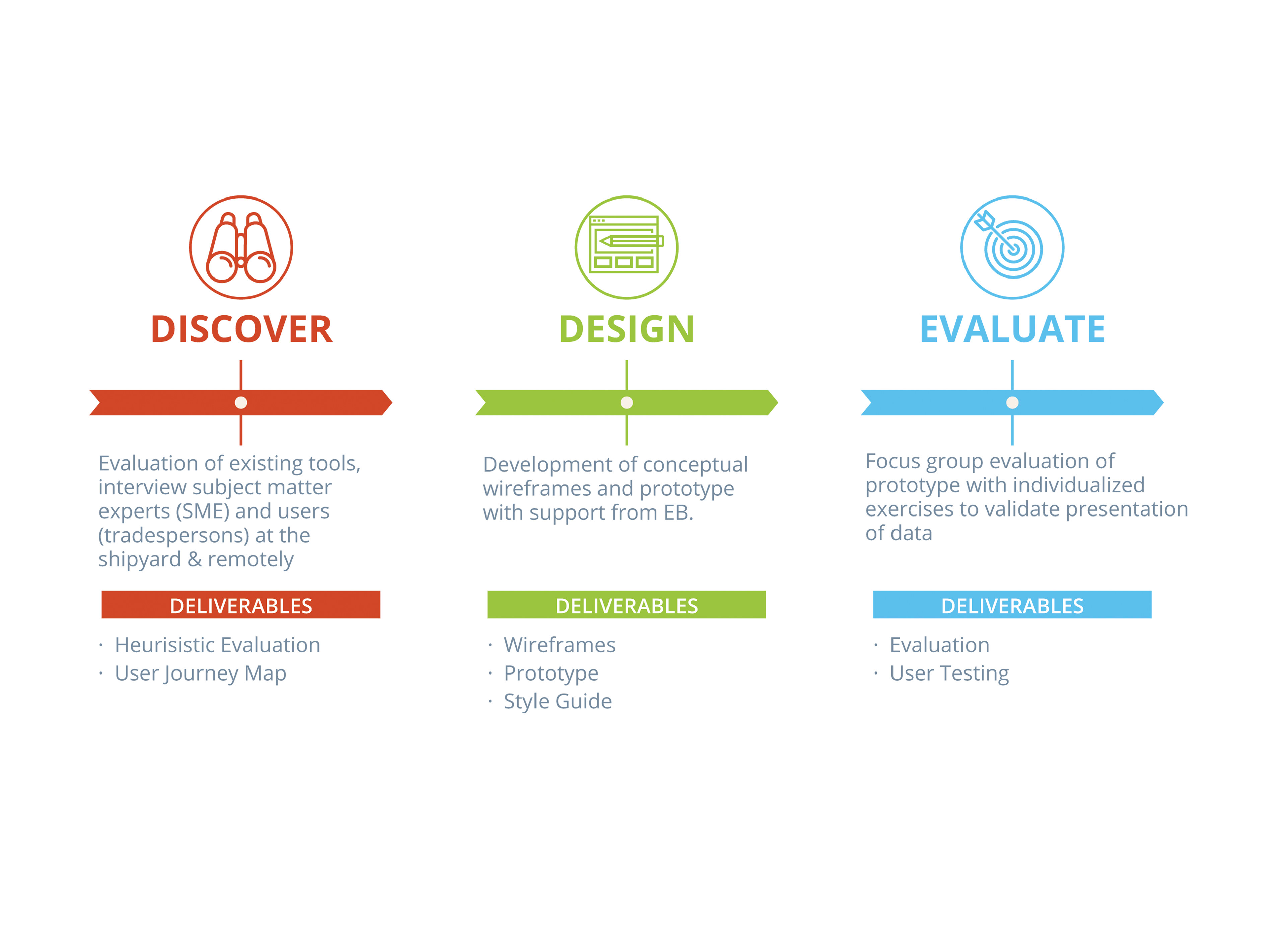
INTEGRATING FEEDBACK
Three 90-minute hybrid focus group/demo sessions were conducted with 26 participants at Quonset Point and Groton. Participants completed a background survey and consent form before evaluating three life-sized printed images of the IWI interface. Using color-coded stickers and a pen, they identified engaging and unclear elements while following a mechanic's typical workflow scenario, from shift muster to retrieving a tablet. Insights from these exercises and discussions guided key design refinements.
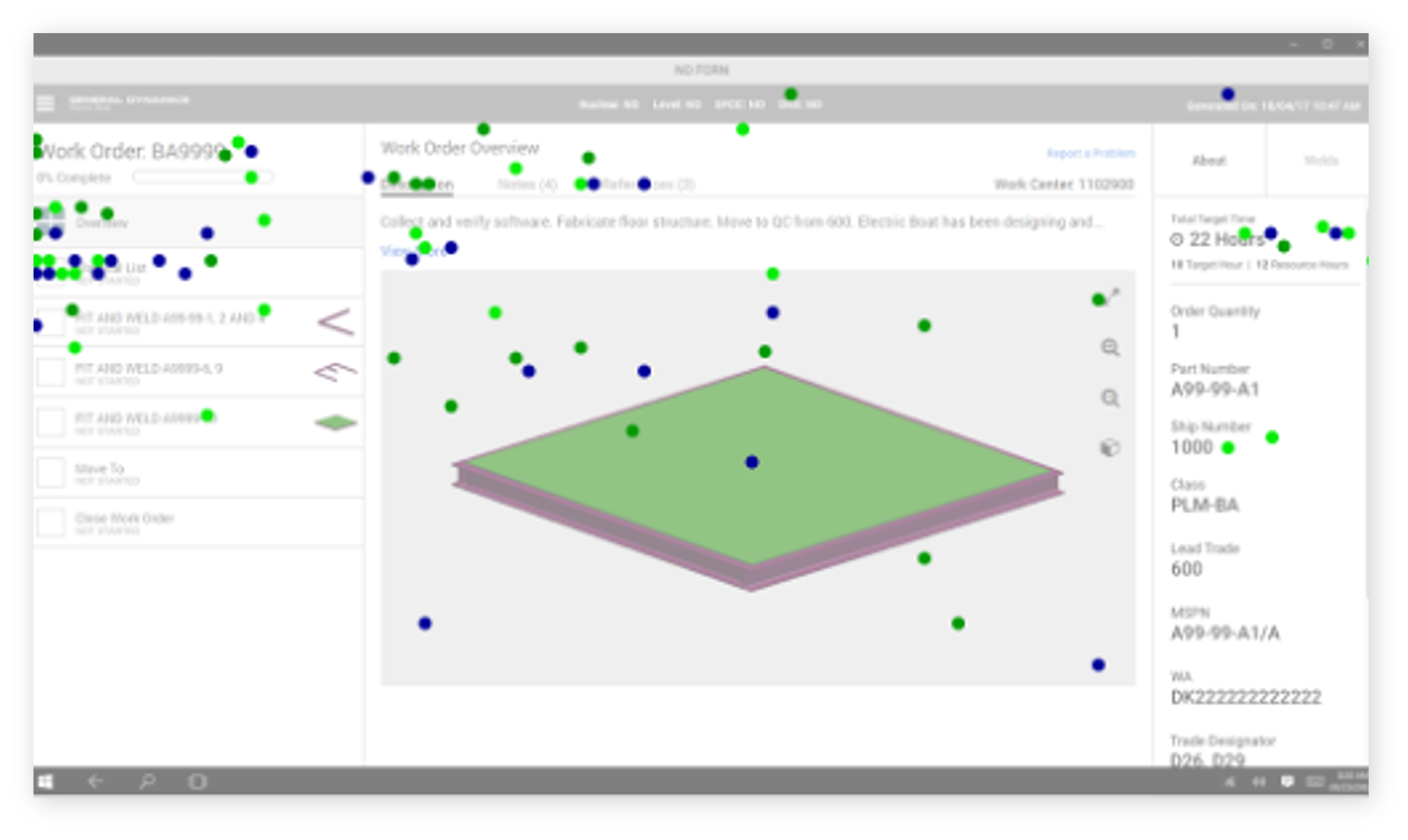
Most important (dark green), second most important (light green), and next tap areas (blue).
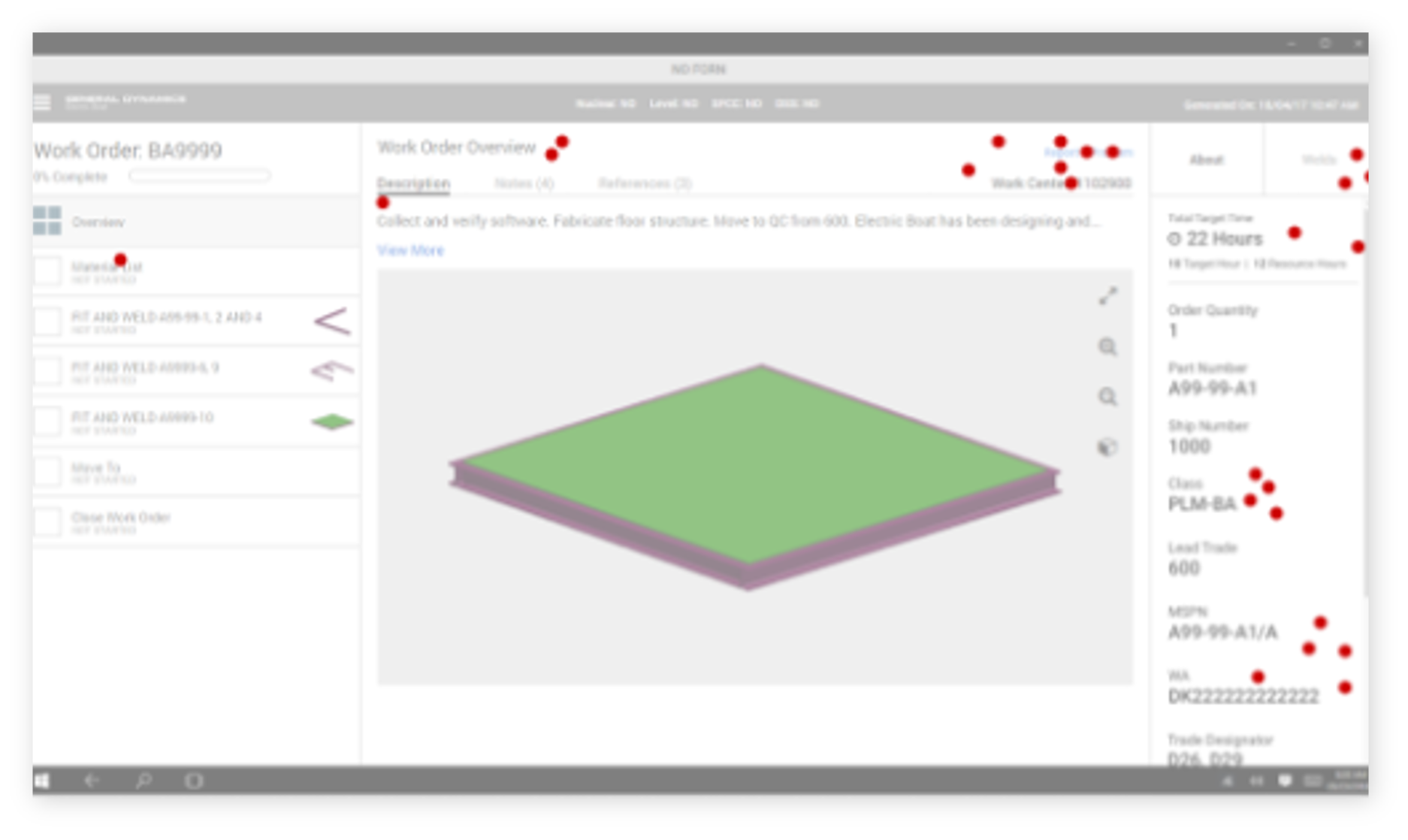
OUTCOMES & IMPACT
Cost Implications of Paper-Based Instructions:
· Transitioning from paper-based to digital work instructions can lead to significant cost savings. For instance, Dozuki reports that the average company uses about 10,000 sheets of paper per employee annually, costing approximately $259.80 per employee each year. For a workforce of over 10,000 tradespersons, this translates to an estimated $2.6 million spent on paper annually. Digitization can substantially reduce or eliminate these costs.
Efficiency Gains from Digital Implementation:
· Our study found that manual repair tasks can be completed 21% faster using digital work instructions compared to traditional paper-based methods.
· Participants reported a 26% reduction in perceived workload when utilizing the digital instructions.
Qualitative Improvements:
· Enhanced Accuracy: Digital instructions can reduce human error by providing real-time updates and ensuring that all personnel have access to the most current procedures.
· Improved Version Control: Digitization ensures that all tradespersons are working from the latest set of instructions, reducing inconsistencies and miscommunications inherent in paper-based systems.
· Environmental Impact: Reducing paper usage aligns with environmental sustainability goals, decreasing the organization's carbon footprint.
FINAL DESIGN
Every work package (also known as work order) has a standard view that enables a tradesperson to navigate through a sequence of operations and relevant information linked with those operations. The left and right panels can be easily hidden or shown with a single tap to prioritize the view.
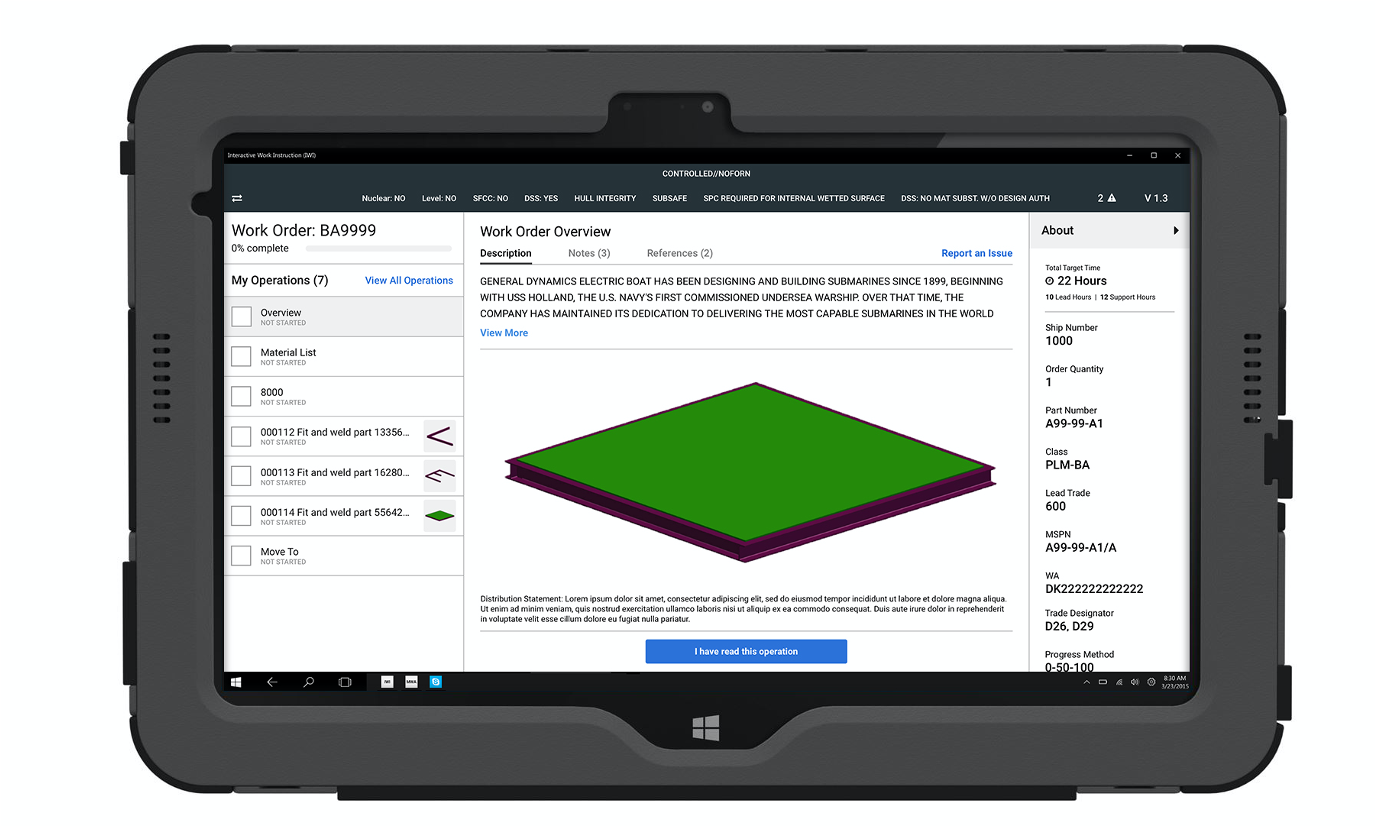
Standard View
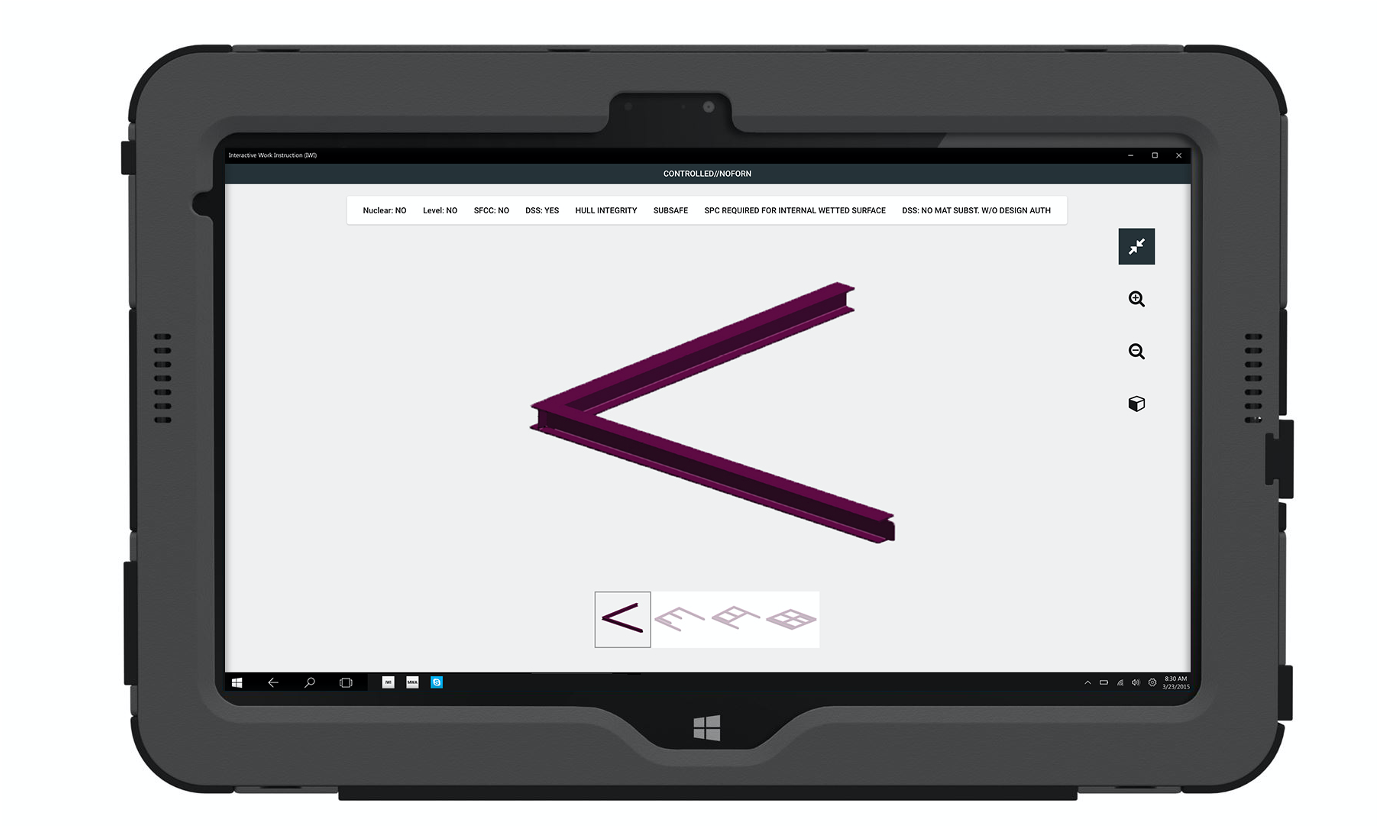
It supports adjustable 2D and 3D views with touchscreen gestures like pinch-to-zoom and carousel navigation.
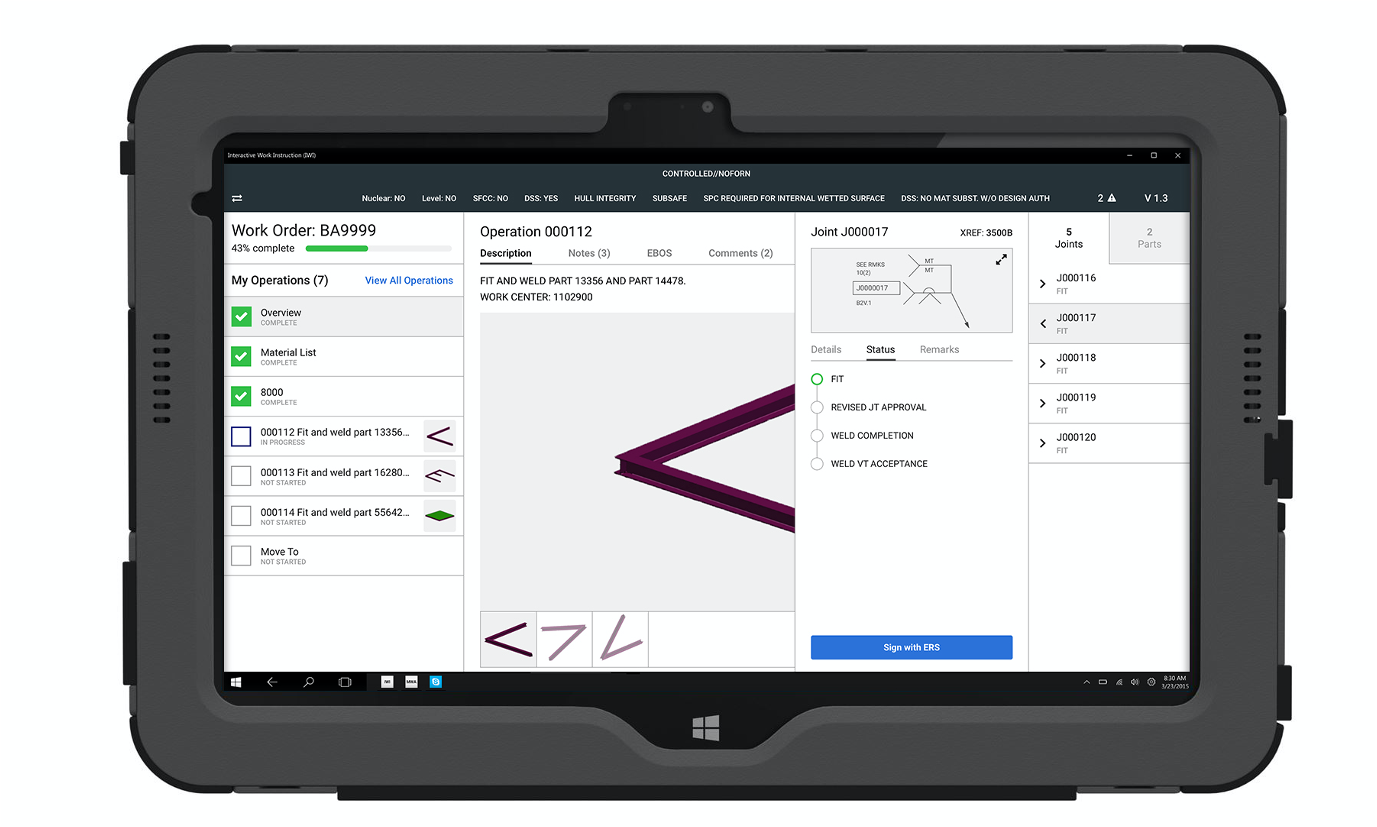
Users can access detailed info and mark tasks complete directly from their tablets, avoiding unreliable kiosks. This enables timely updates, improves accuracy, and helps management plan future tasks more effectively.